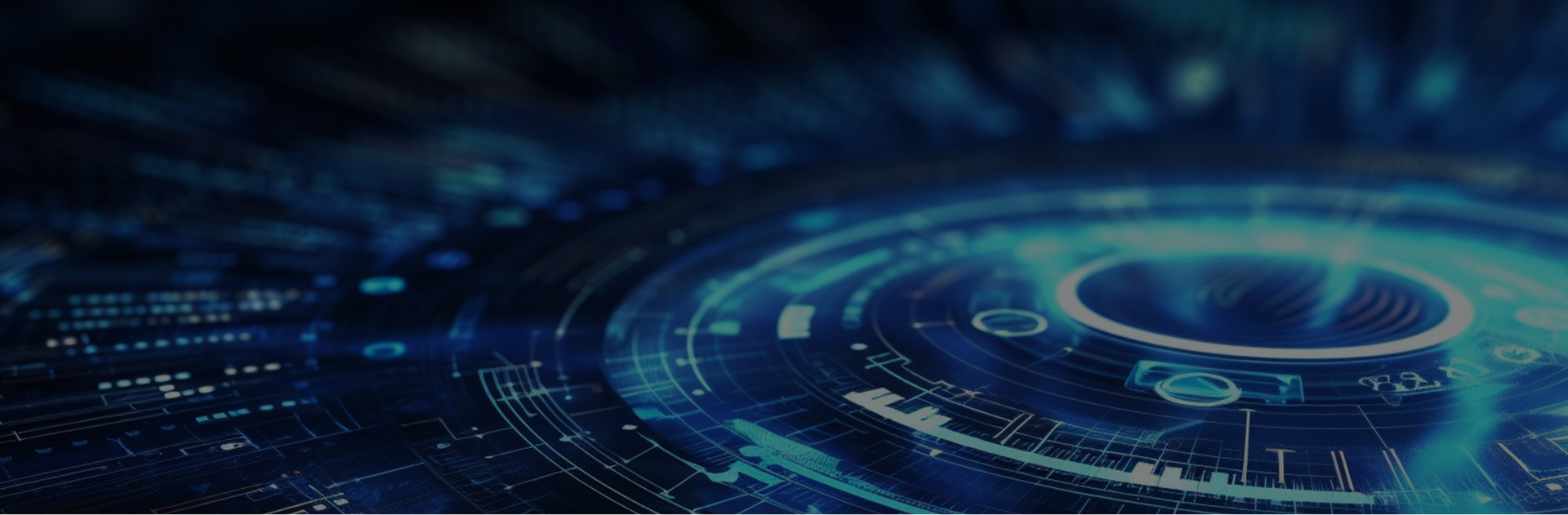
Special Filtration Process
Filtration and Separation Breaking Boundaries in Industrial Innovation
No data
Raney Ni Eletromagnetic Filtration
Raney nickel is an efficient solid-phase catalyst known for its excellent catalytic activity, stability, and thermal conductivity, making it suitable for various hydrogenation reactions. It consists of fine particles of porous nickel-aluminum alloy. This catalyst is typically employed in reactions involving hydrogenation or selective hydrogenation. It finds widespread applications in different fields, such as the preparation of tetrahydrothiophene by hydrogenation of tetrahydrothiophene sulfoxide, synthesis of para-aminophenol by hydrogenation of nitrophenol, production of cycloalkanes by hydrogenation of aromatic rings, conversion of aldehydes and ketones into alcohols, and the synthesis of aryl amines. Raney nickel has been proven to be highly versatile and indispensable in the field of hydrogenation.
Problem
Raney nickel is known for its potential to spontaneously combust when exposed to air, making it a challenging catalyst to handle during the post-reaction separation and filtration process. The traditional method of filtration involves passing the reaction solution through a stainless steel hopper lined with a nylon filter bag, which is then vacuumed into a concentration kettle to remove the catalyst. However, this method poses significant risks as the filter hopper is open, increasing the potential for accidents.
Furthermore, the highly active nature of the Raney nickel catalyst post-reaction makes recycling a desirable option for economic benefits. Unfortunately, the open filtration method oxidizes and deactivates the catalyst, rendering it unsuitable for recycling. This loss of recycling potential further emphasizes the need for a safer and more efficient filtration system in propylene oxide production.
Product Advantages
To overcome the flammability of Raney nickel catalyst during filtration, Feature-Tec utilizes its strong magnetic properties, employing magnetic filtration to separate the catalyst.
The Ferroclean II electromagnetic filtration system efficiently removes ferromagnetic and paramagnetic impurities from various fluids using electromagnetic adsorption principles. It operates in a fully enclosed mode, automating the filling, filtration, and backwashing processes to eliminate risks associated with manual operation. During backflush and backwash, demagnetization control is employed, allowing the catalyst to discharge through the outlet. The liquid forms a protective layer, isolating the catalyst from contact with air, enabling direct recycling of the highly active catalyst.
Case Study
1,4-Butanediol (BDO) is a crucial organic and fine chemical raw material. The Reppe process comprises two main steps: acetylene reaction and hydrogenation reaction, typically employing nickel-based catalysts in the hydrogenation stage. In 2012, a large coal chemical enterprise in Xinjiang initiated a 100,000-ton/year BDO project. They utilized the Feature-Tec Ferroclean II filtration system to filter the reaction product with a mass flow rate of 13,000 Kg/h. The material consisted of 25 Kg/h solid mass, liquid density of 961 Kg/m³, solid density of 920 Kg/m³, and catalyst particle size of 10μm. Post-filtration, the catalyst mass in the material decreased to an average of 1.2 Kg/h, achieving a catalyst recovery efficiency of over 95%.
(Hydrofiltration flow chart)
Toluene diisocyanate (TDA) is a primary raw material for polyurethane. TDA is typically produced through the catalytic hydrogenation of dinitrotoluene (DNT). Catalysts can include Raney nickel, iron, platinum, palladium, and other precious metals.
In 2014, an international multinational chemical company made significant improvements to their Raney nickel catalyst recovery process. They conducted a pilot test using the Ferroclean II filtration system, with a feed volume of 40m3/h, catalyst content of 0.02%, catalyst particles ranging from 3 to 10um, operating pressure of 0.4MPa, and operating temperature of 150℃. After the test, the catalyst recovery rate exceeded 98%. This optimization is estimated to yield substantial economic benefits, resulting in savings of over $3 million per year in catalyst costs.
Applications:
After years of practice, the feasibility, safety and economy of Raney's nickel catalyst magnetic filtration method has been verified, and the Ferroclean Ⅱ electromagnetic filtration system even has filtration effect on weakly magnetic or paramagnetic particles, which can be widely used in the field of chemical catalyst filtration.
Related Solutions
Related components
Related components
Related Equipment
Message consultation
Contact
Hotline: (+86)400-820-6150
Email: marketing@feature-tec.com
Address: 8/F, Block A, Building 3, Tianhua Information Technology Park, 299 Longcao Road, Xuhui District, Shanghai
COOKIES
Our website uses cookies and similar technologies to personalize the advertising shown to you and to help you get the best experience on our website. For more information, see our Privacy & Cookie Policy
COOKIES
Our website uses cookies and similar technologies to personalize the advertising shown to you and to help you get the best experience on our website. For more information, see our Privacy & Cookie Policy
These cookies are necessary for basic functions such as payment. Standard cookies cannot be turned off and do not store any of your information.
These cookies collect information, such as how many people are using our site or which pages are popular, to help us improve the customer experience. Turning these cookies off will mean we can't collect information to improve your experience.
These cookies enable the website to provide enhanced functionality and personalization. They may be set by us or by third-party providers whose services we have added to our pages. If you do not allow these cookies, some or all of these services may not function properly.
These cookies help us understand what you are interested in so that we can show you relevant advertising on other websites. Turning these cookies off will mean we are unable to show you any personalized advertising.